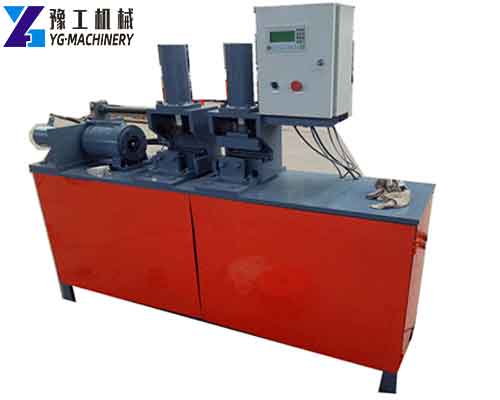
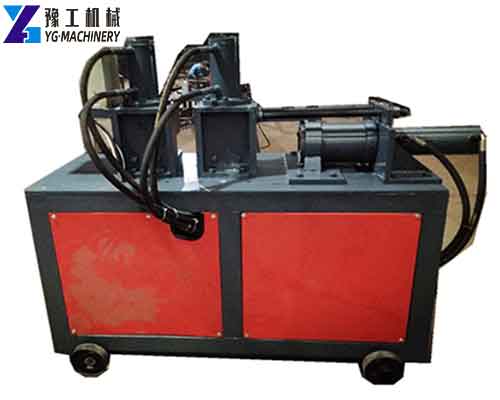
The pipe shrinking machine is a hydraulic automatic pipe end processing machine that controls the end surface of the pipe under normal conditions and is controlled by an integrated control touch screen. The mold can be expanded, shrank, bulged, and smashed. The pipe ends are processed and formed, and the manual, jog, or automatic machining machine can be freely determined according to the user’s needs. The fuel tank, the bed, the slider, the main cylinder, the mold core rod (optional), the limit cylinder, the compression cylinder main components such as the clamping die axial positioning cylinder, and axial positioning angle iron. In addition, we also have rebar straightening and cutting machines, rebar threading machines, steel bar cutting machines, rebar bending machines, steel hoop bending machines, rebar upsetting machines, beam bending machines, rebar derusting machines, hydraulic combined punching and shearing machines, stirrup bending machines, chain link fence machines, etc. Contact us now to know more.【WhatsApp/WeChat/Skype/Phone】+86 136 1385 6800
Parameters of Hydraulic Pipe Shrinking Machine:
Product Name | Hydraulic Pipe Shrinking Machine |
Model | Hydraulic-3 cylinder |
Pipe Diameter | 20-60mm |
End Straight | Max120mm |
Pipe Thickness | 1.5-3mm |
Motor | 3 kW |
Voltage | 380V,50Hz,3 phase |
Working Speed | 3000-5000pieces/day |
Weight | 600 kg |
Packing Size | 1800*700*1800mm |
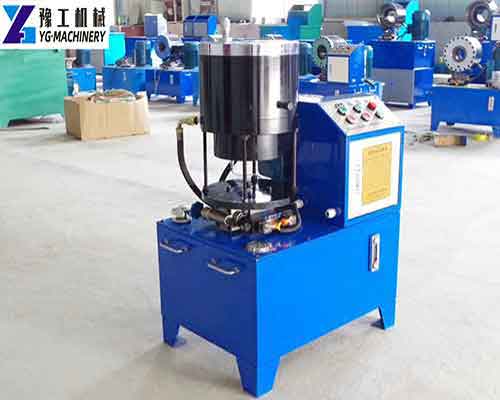
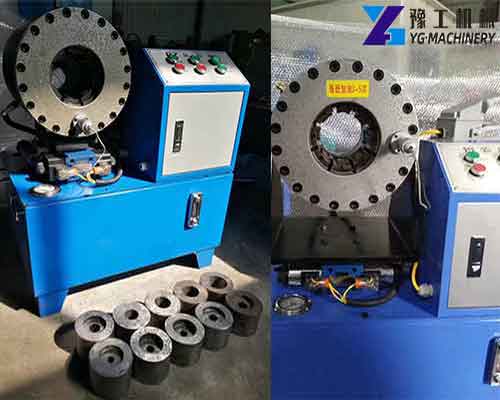
Application of YG Pipe Shrinking Machine:
The pipe shrink machine is widely used in the processing and forming of pipe joints, automobile oil pipes, air pipes, water pipes, air-conditioning pipes, etc. It is an ideal pipe end forming processing equipment, and the processing shapes include convex, concave, long flat, square, extension oblique, V-shaped, open elbow, flat elbow, etc. manufactured into molding molds according to the product.
Pipe Shrinking Machine Description:
Pipe shrinkage is a molding process that reduces the diameter of the end of the tube blank. The tube blank enters the deformation zone by the axial force, produces a tangentially shrinking plastic deformation in the deformation zone, and then enters the stable zone, eventually forming a reduced end diameter.
Pipe flaring is a forming process for expanding the diameter of the end of the tube blank. The flared shape can be tapered or cylindrical. The pipe blank enters the deformation zone under the axial force and produces tangential stretching in the deformation zone. The flaring is plastically deformed, and then enters the stable deformation zone and is finally formed.
By setting the tubular throttle valve on the main cylinder circuit, the working speed of the main cylinder can be adjusted; the superimposed hydraulic control check valve is arranged on the compression cylinder, thereby ensuring that the mold clamping process is not loose; the displacement cylinder a superimposed two-way throttle valve is arranged on the limit cylinder and the axial positioning cylinder circuit to adjust the two-way movement speed of the above cylinder. The shifting cylinder and the limiting cylinder cooperate with the conversion station so that the station conversion is convenient and accurate, and the processing quality of the pipe fitting is ensured.
Steel Tube Shrinking Machine Working Principle:
Through mechanical transmission, the steel pipe is rotated and heated by a flame at one end of the steel pipe. When a certain temperature is reached, the heated steel pipe head is smarted by a molding die until the desired shape is reached.
Construction:
Weld a ground plate with channel steel. The power end is equipped with a motor, reducer, and chuck (the card tube, can be replaced by a lathe chuck). The other end is equipped with a support seat (openable), and the outer end of the support base is fixed with a heating ring (8-10 nozzles, which are welded to the copper pipe ring by gas welding). At the outermost is an active bracket with an alloy mold mounted on it.
How to use: Fix the tube on the tube shrinker and turn on the heater (ring). After the temperature is reached, the alloy mold is pushed and the shape of the tube head meets the requirements. The whole process takes about 15 minutes.
Tube Shrinking Machine 11 Operating Procedures:
- Check the oil mark before the operation, not lower than the oil mark, and lubricate the guide rail.
- Start the hydraulic oil pump, the system oil pressure should not exceed 40kg/cm2.
- After the system oil pump and speed are adjusted, do not adjust it at will.
- When the room temperature is lower than 0 degrees Celsius, first start the hydraulic oil pump and use it after 10 minutes of dry running. When the oil temperature is higher than 55 degrees Celsius, cooling measures should be adopted.
- Always check for looseness on the travel switch to prevent accidents.
- The shrinkage head mold should be removed and cleaned frequently to prevent excessive impurities and difficulty in disassembling.
- When operating, concentrate your thoughts, and don’t talk to others to avoid accidents.
- When working, always add fuel to the guide rails, no less than 5 times per shift.
- When shutting down, first turn off the spindle, then turn off the oil pump.
- After the work is finished, cut off the power supply and clean the machine and the surrounding area.
- According to the company’s equipment management system, the tube shrinking machine is regularly inspected and maintained to ensure safety and reliability during use.
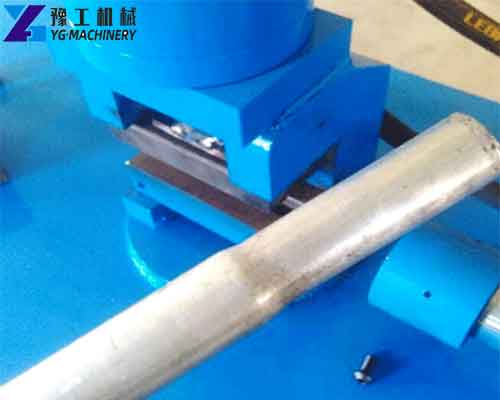
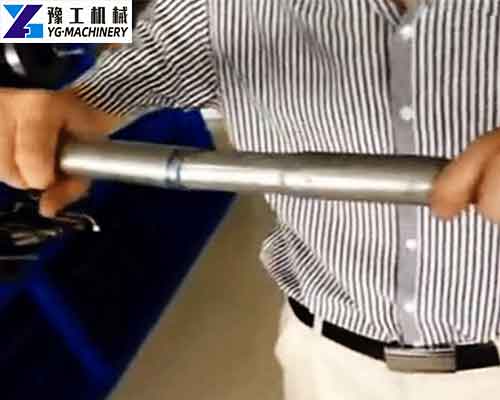
5 Maintenance Pipe Shrinking Machine:
- Always keep the front cone of the shrinking machine head lubricated at least twice a day.
- Always clean the front taper of the shrinking machine head to prevent dirt from entering the machine head and keep the oil clean.
- Check whether the motor or circuit is abnormal. If it is, it should be excluded.
- View the fuel tank through the oil window and the oil quantity is in place.
- Check the motor and clean the surface with no dust or oil. The screws of each part are fully fastened, the windshield and the blades are not damaged, and the casing has no cracks.
General Troubleshooting:
1. Fault: The cylinder does not move after starting.
Reason: Check that the motor steering is in line with the oil pump steering and that the flow valve handle is loose.
Remedy: Adjust the motor steering to match the oil pump steering.
2. Fault: There is no pressure in the cylinder.
Cause: Check the plunger pump ( gear pump), check the relief valve, and check the cylinder.
Remedy: Adjustment or replacement.
3. Fault: The system is noisy.
Cause: Check the plunger pump, check if the oil filter is blocked, and if the hydraulic oil meets the requirements.
Remedy: Replace the oil filter and hydraulic oil.
Pipe Shrinking Machine Manufacturer – YG Machinery
As a professional manufacturer of various types of machinery, we also have other production lines, wet wipes machines, shoe cover-making machines, paper cup-making machines, double wall paper cup machines, paper bowl-making machines, paper dish-making machines, paper straw-making machines, folder gluer machines, roll die cutting machines, paper cup printing machines, you can send us an email from link page for a quotation now. And if you are interested in other kinds of machinery in our company, you can visit the appropriate page to check more or contact us directly. We will reply to you in 24 hours.【WhatsApp/WeChat/Skype/Phone】+86 136 1385 6800