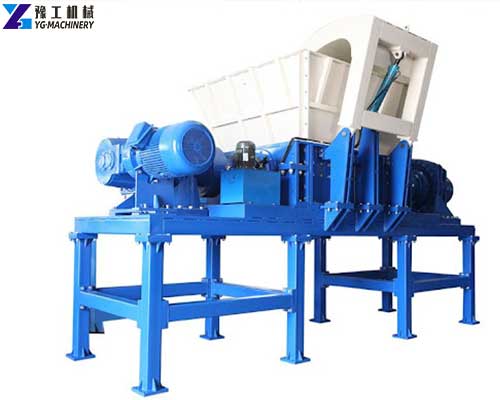
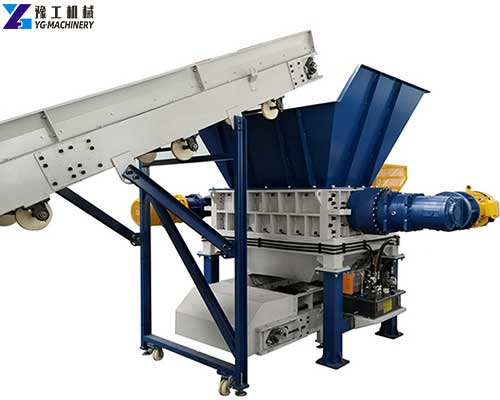
An industrial metal shredder is a kind of equipment specially used for processing various scrap metals. It can break the metal parts of scrap cars, electronic products, industrial waste, etc. into smaller and more regular particles, which are convenient for subsequent classification, recycling, and reuse. Metal shredder mainly cuts, tears, and squeezes materials through high-speed rotating knives to achieve the purpose of crushing. According to the number and arrangement of knives, they can be divided into single-axis shredders, double-axis shredders, and four-axis shredders. Its selection directly affects the enterprise’s production efficiency and cost. Today, we will explain the key points of purchasing an industrial metal shredder from multiple angles to help you choose the most suitable equipment.【WhatsApp/WeChat/Phone/Skype】+86 136 1385 6800
Industrial Metal Shredder Parameter:
Model | YG-600 | YG-1000 | YG-1200 | YG-1500 | YG-1800 |
Knife size(mm) |
Φ200*20 | Φ300*30 | Φ300*40 | Φ500*50 | Φ600*60 |
Power (kW) | 11*2 | 37*2 | 45*2 | 75*2 | 90*2 |
Capacity(t/h) | 0.3-0.5 | 1-1.2 | 2.5-3 | 3.8-4.5 | 6-7 |
Knife quantity(pcs) |
30 | 26 | 30 | 38 | 45 |
Machine size(m) |
2.6*1*2.1 | 3.4*1.25*2.2 | 3.8*1.25*2.2 | 4.4*1.5*2.5 | 5.3*2.1*2.8 |
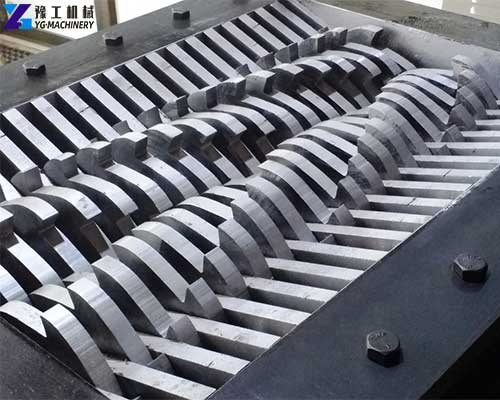
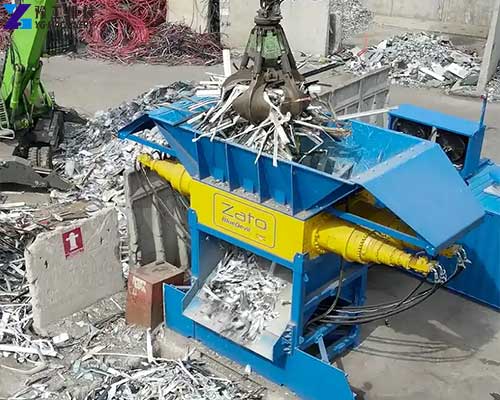

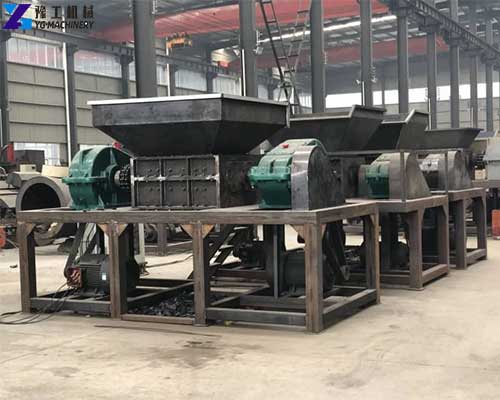
Industrial Metal Shredder Buying Guide: Choose the Right Equipment to Improve Efficiency
1. Clarify your needs and determine the type of equipment
Before purchasing an industrial metal shredder, you must first clarify your needs:
- Material type: Metals of different materials such as scrap steel, scrap aluminum, and scrap copper have different requirements for the equipment’s knives, speed, etc.
- Material size: Materials of different sizes such as large pieces of scrap steel and small pieces of aluminum chips have different requirements for the size of the feed port and the structure of the shredding chamber.
- Processing capacity: The number of tons of materials processed per hour determines the power and size of the equipment.
- Output particle size: The particle size requirements for the final product affect the selection of knives and the configuration of the screen.
- Special requirements: Are there any special noise, dust, etc. requirements?
Based on the above needs, the following common types of industrial metal shredders can be determined:
- Single-axis shredder: Simple structure, low cost, suitable for processing softer metals and medium-sized materials.
- Double-axis shredder: Complex structure, higher efficiency, suitable for processing metals with higher hardness and large materials.
- Four-axis shredder: Complex structure, highest efficiency, suitable for processing metal materials of various complex shapes and hardness.
2. Pay attention to equipment performance indicators
- Shredding capacity: refers to the amount of material that the equipment can process per hour, which is related to factors such as motor power, number of cutters, and speed.
- Shredding particle size: refers to the particle size of the material output by the equipment, which can be adjusted by replacing the screen.
- Motor power: The motor power determines the shredding capacity of the equipment. The greater the power, the stronger the shredding capacity.
- Cutter material: The cutter material determines the wear resistance and service life of the equipment. High-hardness alloy steel is generally used.
- Noise level: Too high noise level will affect the working environment. Low-noise equipment should be selected.
3. Compare products from different manufacturers
- Cost-effectiveness: Choose a company with high cost-effectiveness and a good reputation.
- Product quality: Carefully check the material, processing accuracy, and appearance of the equipment.
- After-sales service: Understand the manufacturer’s after-sales service policy, including warranty period, spare parts supply, etc.
- Price: Consider the performance and price of the equipment comprehensively and choose products with high cost-effectiveness.
4. On-site inspection and trial machine acceptance
- On-site inspection: Go to the manufacturer or dealer to inspect the equipment on-site and understand its operation.
- Test machine acceptance: Test the machine on site to check the shredding effect, noise level, etc. of the equipment.
5. Precautions
- Safety protection: The equipment should be equipped with complete safety protection devices, such as an emergency stop button, protective cover, etc.
- Installation environment: The installation site of the equipment should be flat, solid, and have good ventilation conditions.
- Daily maintenance: Regularly inspect and maintain the equipment to extend the service life of the equipment.