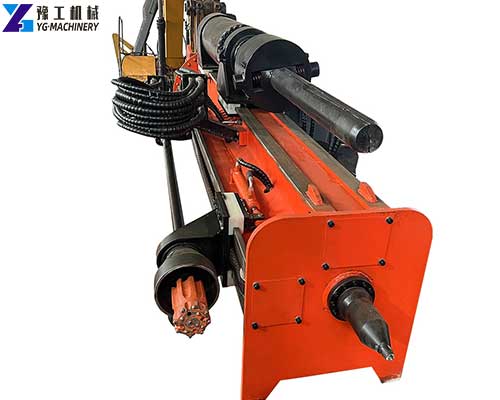
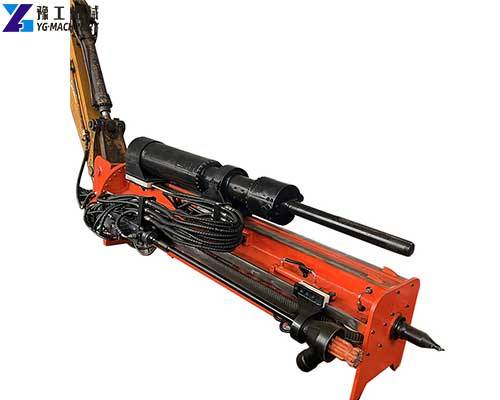
The integrated drilling and splitting machine is a kind of engineering machinery that integrates the functions of drilling and splitting. It directly installs the rock drill and splitter on the excavator or other engineering machinery and realizes the drilling and splitting work through the hydraulic system. This integrated design greatly improves work efficiency and reduces construction costs. It is an advanced technology in the field of rock crushing. Do you also want to use this machine to improve your project efficiency? Contact us.【WhatsApp/WeChat/Phone/Skype】+86 136 1385 6800
Integrated Rock Drill and Splitter Parameter:
Rock Drilling Machine | |||
Power | Drilling hole diameter | Drilling depth | Drilling speed |
24kw | Middle 120mm | 1600mm | 1m/min |
Splitting Machine | |||
Splitting depth | Splitting force | Rotation angle | – |
1000MM | 8000T | 120° | – |
Push Beam | |||
Rock drilling maximum propulsion | Splitting maximum pullout force | ||
25KN | 70KN | ||
Excavator requirements:>25T |
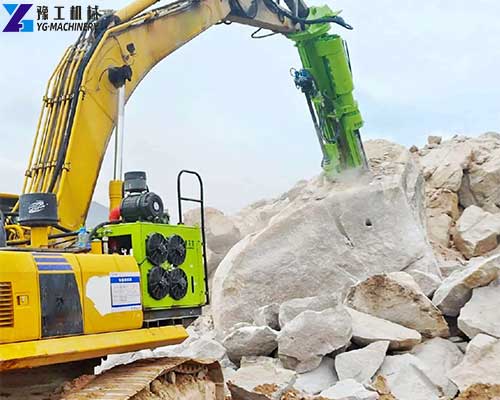
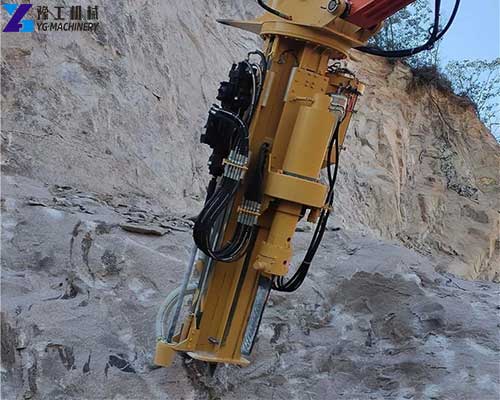
Selection of Drilling and Splitting Machine:
- Rock hardness: Select different types of drill bits and split wedges according to the hardness of the rock.
- Hole diameter and depth: Select appropriate drilling parameters according to construction requirements.
- Working environment: Consider factors such as working space, terrain, and climate.
- Engineering machinery: Select matching engineering machinery.
The Basis for Selecting a Suitable Drilling and Splitting Machine:
1. Rock characteristics
- Rock hardness: The hardness of different rocks varies greatly, so it is necessary to select equipment with corresponding hardness for the drill bit and splitting wedge.
- Rock fissures: The degree of development of rock fissures will affect the effect of drilling and splitting, and the adaptability of the equipment needs to be considered.
- Rock stratification: Rock stratification will affect the direction and depth of drilling, and needs to be adjusted according to actual conditions.
2. Engineering requirements
- Crushing degree: According to engineering requirements, select the appropriate crushing degree to achieve the desired effect.
- Aperture and depth: According to engineering needs, select appropriate drilling parameters.
- Working environment: Consider factors such as working space, terrain, and climate, and select equipment with strong adaptability.
- Construction progress: According to construction progress requirements, select equipment with high work efficiency.
3. Equipment performance
- Power system: Ensure that the equipment’s power system can meet the power requirements of drilling and splitting.
- Hydraulic system: The hydraulic system should be stable and reliable to ensure the output of splitting force.
- Control system: The control system should be simple to operate and easy to control.
- Durability: The equipment should have high durability and be able to adapt to harsh working environments.
4. Economic factors
- Equipment price: Choose the appropriate equipment according to the budget.
- Operation cost: Consider the energy consumption, maintenance costs, etc. of the equipment.
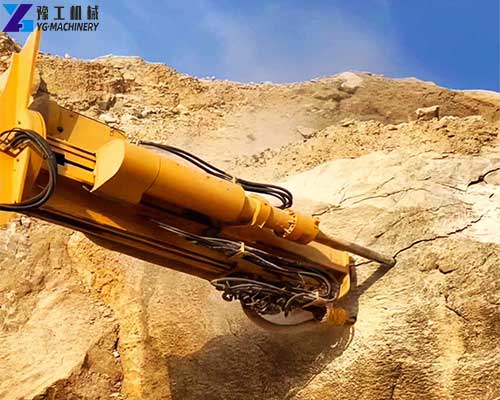
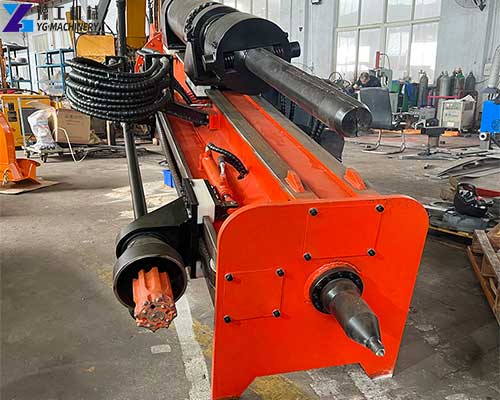
Integrated Rock Drill and Splitter Manufacturer – YG Machinery
As a new type of rock mining equipment, the integrated rock drilling and splitting machine significantly improves operating efficiency and flexibility by combining drilling and splitting functions. This design not only simplifies the operating process and reduces equipment switching time, but also effectively reduces construction costs. This innovative solution brings new development opportunities to the rock mining industry and is expected to promote the innovation of traditional rock mining methods. Of course, we also have small rock splitters, gasoline rock drills, down-the-hole drills, excavator hydraulic breakers, and other equipment to meet your different needs.【WhatsApp/WeChat/Phone/Skype】+86 136 1385 6800